Associate Professor Yee Fook Cheong is shaping the future of manufacturing as the first Academia Fellow of the International Centre for Industrial Transformation.
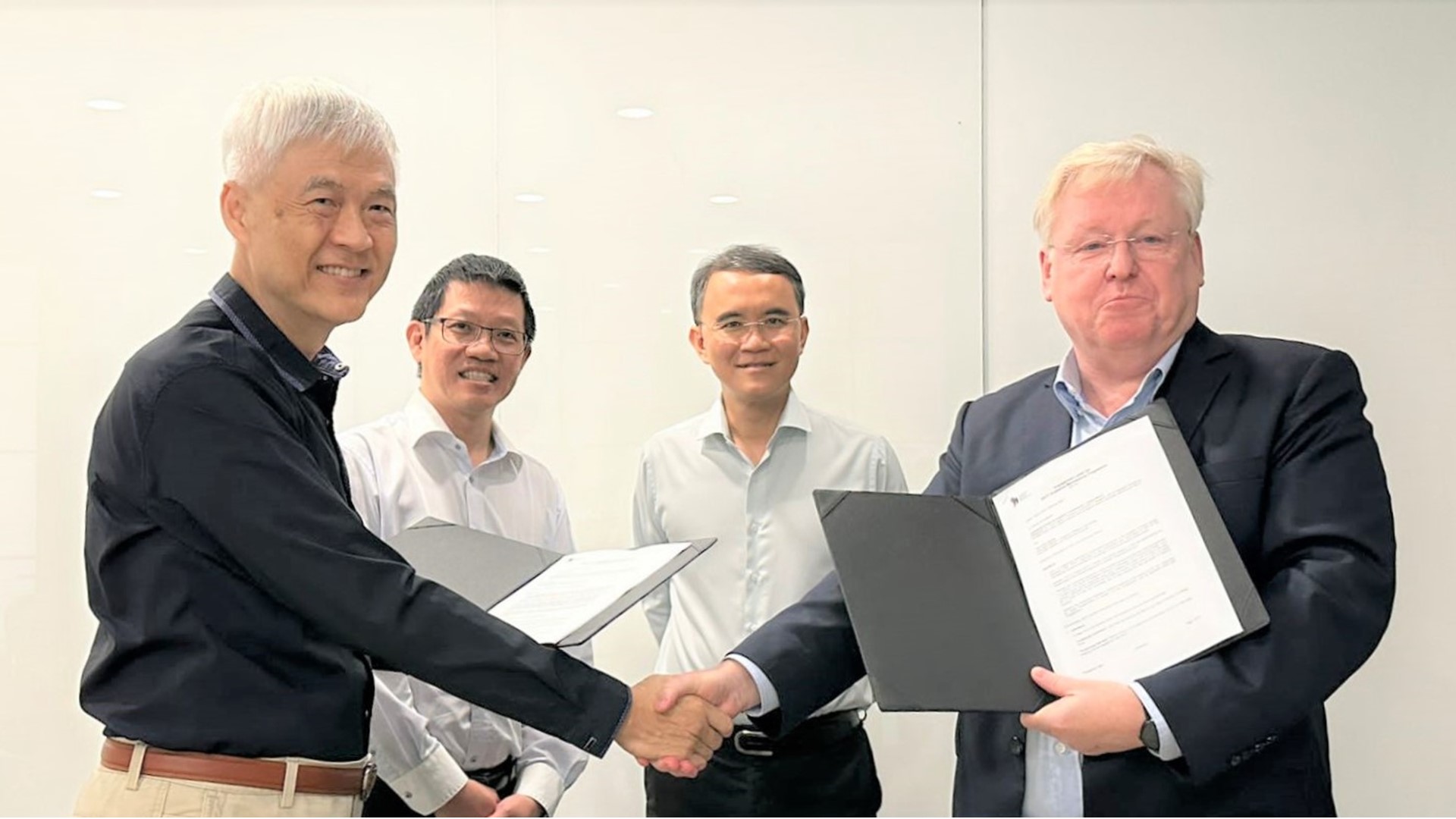
(From left) A/Prof Yee Fook Cheong; Associate Professor Kenneth Low, Cluster Director, Engineering, SIT; Professor John Thong, Deputy President (Academic) and Provost, SIT; and Raimund Klein, INCIT’s Founder and CEO, at the appointment ceremony of A/Prof Yee as Academia Fellow at INCIT in March 2023. (Photo: Kevin Foo, INCIT)
Associate Professor Yee Fook Cheong’s dream has always been to be a mechanical engineer. In his youth, he would tinker with appliances like clocks and became a scout to build wooden structures.That dream continues today on a much larger scale, as he aims to shape the future of manufacturing by digitalising it in the era of Industry 4.0. As a faculty member from the Engineering Cluster at the Singapore Institute of Technology (SIT), his projects include creating digital twins for manufacturing processes and creating more efficient platforms to provide “manufacturing-as-a-service” across countries.
His appointment as the first Academia Fellow of the International Centre for Industrial Transformation (INCIT) in March this year will enable him to transform not just Singapore’s manufacturing scene, but the sector’s global landscape.
“This appointment allows me to showcase Singapore's contributions in advanced manufacturing internationally and grow SIT's applied research partnerships with the industry, not only in Singapore but globally,” said A/Prof Yee.
Airbnb of Manufacturing

A/Prof Yee (extreme left) with SIT students at the Industrial Transformation Asia-Pacific 2019 conference. (Photo: Yee Fook Cheong)
One way A/Prof Yee is doing so is by creating platforms that link manufacturing nodes – think of it as an Airbnb equivalent for the sector.Travel has been made easier today. With online marketplace platforms like Airbnb, one can waltz into a welcoming home from Indonesia to Iceland, replete with Wi-Fi, cooking amenities, and even swimming pools. Technology has revolutionised the traveller experience.
In his capacity at INCIT, a non-profit entity championing manufacturing transformation worldwide, A/Prof Yee aims to drive similar innovation in advanced manufacturing by developing use cases and frameworks.
With digital modelling where physical factory processes are reflected on software, it is easier to create a platform for manufacturing companies to list their capabilities, services and availability.
Original equipment manufacturers (OEMs) that often produce or assemble components manufactured across countries and regions can scroll through these “listings”. For instance, an aerospace company might want to manufacture an engine component in Singapore, aircraft doors in Vietnam and motorised actuators in China.
The platform can filter out the capability and availability of the listed factories, balancing demand and supply through artificial intelligence (AI). “If you can maximise that, you can lower the cost of manufacturing, have better access to new technologies and improve time to market,” he said. “OEMs can just buy services – it becomes manufacturing-as-a-service. It allows the industry to distribute and share the most critical resources in manufacturing today. It helps to reduce the investment burden for smaller companies, enables the use of resources more sustainably and lowers the barrier of entry for companies that want to capitalise on new technologies.
Making a Change with Digital Technologies
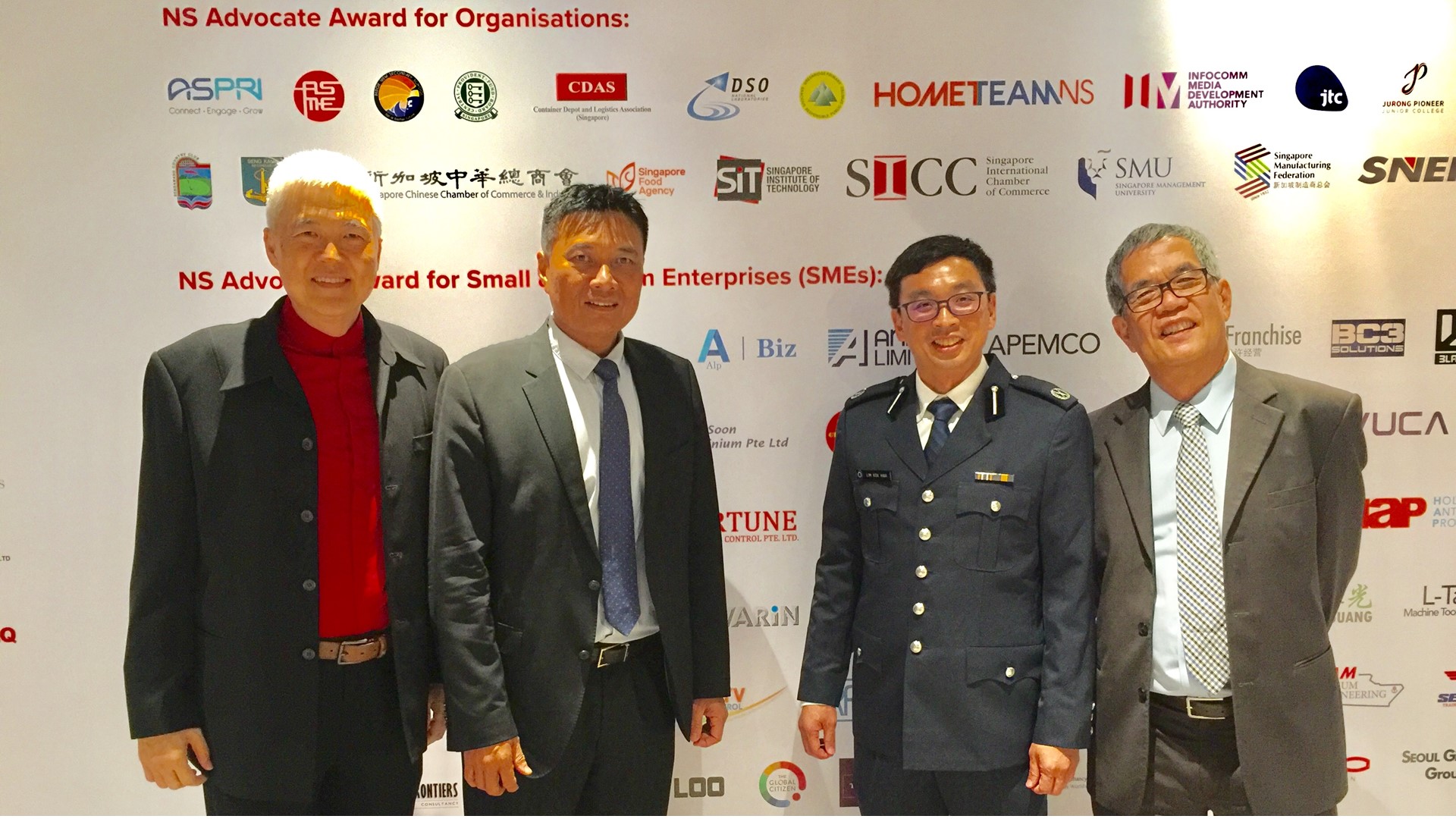
(From left) A/Prof Yee; Mr Abu Bakar bin Mohd Nor, member of SIT’s Board of Trustees; A/Prof Lim Kok Hwa, Director, Professional Officers Division, SIT; and Prof Tan Thiam Soon, Institute Professor, SIT at the Total Defence Awards 2019. (Photo: Yee Fook Cheong)
The next step after digital modelling is digital twinning, where physical processes are not just replicated on software but also recreated virtually as a digital replica, mimicking its functionality and behaviour in real-time. “This is a game-changer,” says A/Prof Yee, “as it could model potential problems and even do AI-driven predictive maintenance.”“For a long time, manufacturing has been very much a brick-and-mortar operation,” he said. “If we can create a digital twin, there are countless opportunities to manufacture more efficiently, productively and cost-effectively.”
Digital twinning has already made its mark in SIT during the COVID-19 pandemic. During the circuit breaker, students from the Mechanical Design and Manufacturing Engineering programme could continue laboratory activities from home via the S.I.T. Learning Factory, a community of smart machines that are interconnected via machine-to-machine communications and remote access technologies designed by SIT professors. This enabled students to remotely conduct their laboratory experiments and monitor operational and control processes using their home computers.
“That is one very tangible result of applied research in the digitalisation of manufacturing Industry 4.0 that we have been doing in SIT,” said A/Prof Yee.
Spurring Green Change
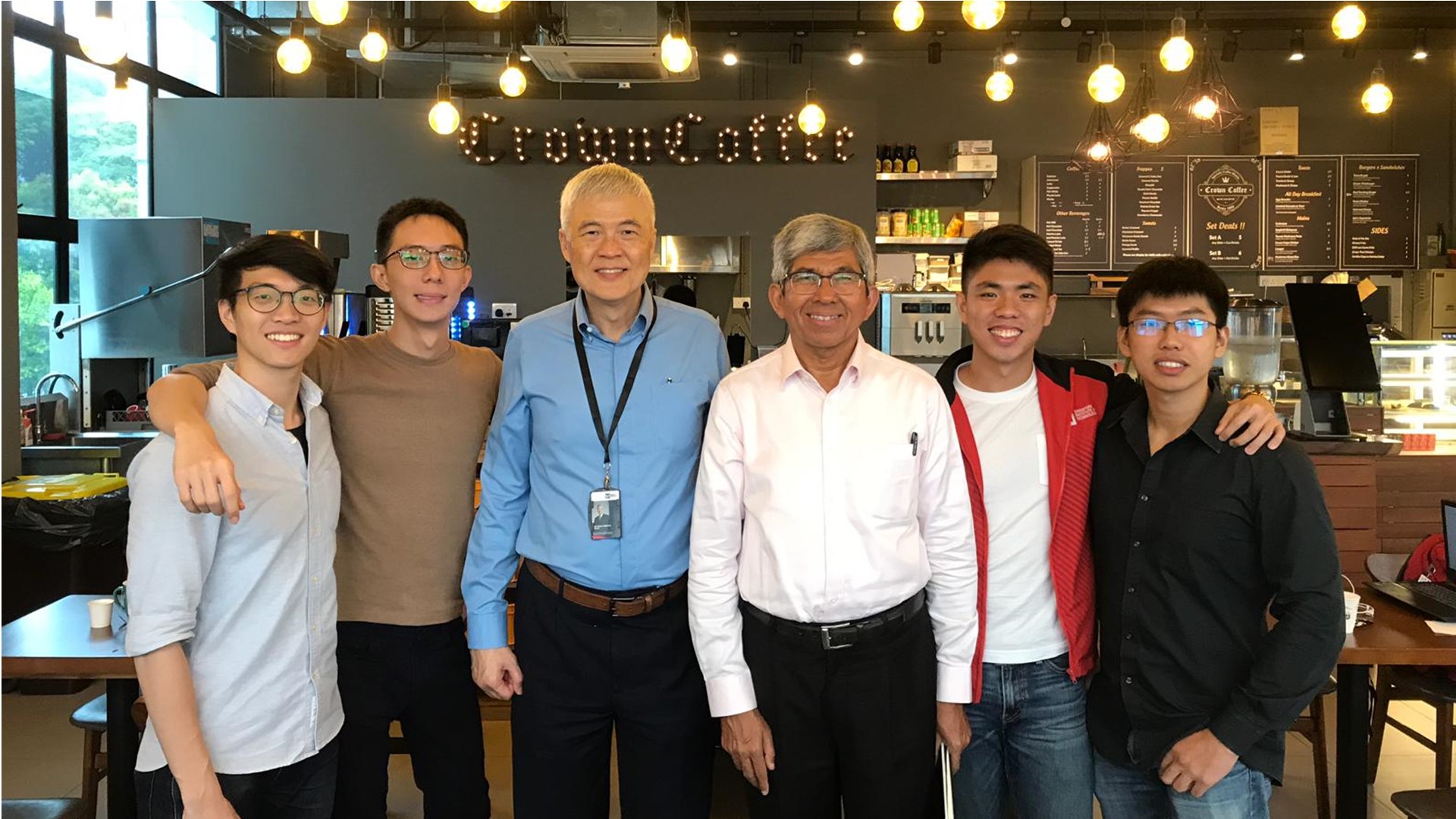
A/Prof Yee (third from left) with Prof Yaacob Ibrahim, Director of Community Leadership and Social Innovation Centre (CLASIC) at SIT (third from right), and SIT student leaders. (Photo: Yee Fook Cheong)
Yet, it is not just about making manufacturing faster, cheaper and better, but also greener. After all, the manufacturing sector produces a fifth of the world’s carbon emissions.[1] A/Prof Yee, who does not have air-conditioning at home for environmental reasons, said it is a “personal passion” of his to reduce the manufacturing industry’s carbon output.At INCIT, he does this by developing transformation frameworks to boost sustainability in manufacturing. An example of such a framework developed in Singapore is the Consumer Sustainability Industry Readiness Index (COSIRI), which assesses the sustainability maturity of companies. Investors and clients can scan the QR code associated with the company’s COSIRI result, which reveals the product’s environmental footprint and allows them to make informed decisions on their investment or purchase.
This might provide a much-needed pinch in the pockets of less green companies. “There’s a lot of work to be done on the sustainability front because manufacturing companies are not thinking much about this at this point in time,” said A/Prof Yee, who has introduced COSIRI to industry players in France, Turkey and Malaysia. Manufacturers are facing challenges as a result of the geopolitical tensions between the United States and China, disruptions in the supply chain, and the transformation to Industry 4.0.
Such industry relevance is central, said the 63-year-old, who joined SIT in 2013 as Vice President (External Relations) as the university’s conduit to the sector. He noted how companies often lack skills development capabilities. SIT’s role is to fill this gap.
He believes his most valuable contribution as an educator is to share his vast experience, while still allowing students to think on their own.
“We translate industry capabilities into skill sets and teach them to students. That is, I believe, our strongest selling point in SIT,” said A/Prof Yee, who also mentors young technopreneurs.
[1] https://www.weforum.org/impact/carbon-footprint-manufacturing-industry/