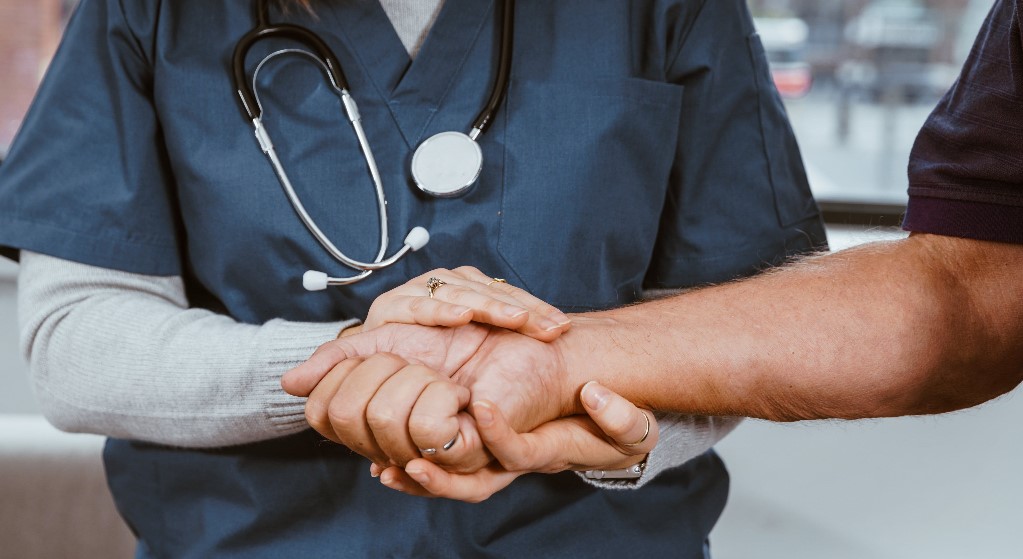
With over 120,000 outpatient consultations every year, the National Heart Centre Singapore (NHCS) took on a multi-faceted approach in enhancing its patient experience under the Lean Skills Development Programme (LSDP), a Lean Thinking programme delivered by SIT in partnership with the Lean Global Network.
According to Lean Thinking principles, the ideal state to strive for is a continuous flow in the process, without problems or bottlenecks preventing the provision of care from reaching patients. Building such principles into the daily work at NHCS would thus complement the Centre’s ongoing quality improvement initiatives.
Collect medicine in 30 minutes or less
One of its first projects was to reduce patients’ waiting time when collecting medication at the Centre’s pharmacy, which may stretch beyond 30 minutes.
Applying Lean Thinking principles, NHCS began mapping the medication dispensing process – from medical order to dispensing – using the A3 methodology. This involved summarising the main elements of a problem-solving exercise on an A3-sized sheet of paper, which included analysing the reasons for the long wait time, identifying wastes from these processes and brainstorming ideas for improvements.
Principal Clinical Pharmacist Manager, Ms Hon Jin Shing, who was concerned for her overworked staff, showed great enthusiasm towards adopting Lean Thinking methodology. Throughout the project, Ms Hon and her team were given lots of flexibility by the LSDP coach from SIT to investigate and implement countermeasures to address these long wait times.
One discovery was that staff had to search for drugs around the whole store in order to fulfil an order. This was inefficient and unproductive, which added to the wait times of patients.
Through Lean Thinking, the team found that dispensing medication could be quicker and more seamless using an assembly-line-like model: by passing an order basket through the different sections of the store. Besides reducing the number of times staff bumped into each other in tight spaces, staff could focus on picking drugs from their designated sections before moving the order along. This reduces the time taken to fulfil each order.
To prevent bottlenecks and ensure a balanced load for each station, the team further used the Glenday Sieve analysis tool to identify the top 15 drugs by volume of sales, and redistributed them evenly across the four picking areas.
This new workflow significantly reduced wait times for patients. In fact, the team exceeded its target of serving 95% or more patients within 30 minutes in some of the months that followed. Through Lean Thinking, the team was able to increase patient satisfaction and put their resources to better use.
Lean Thinking and the A3 methodology were also embraced and embedded in the team’s work culture henceforth. Whenever staff had a problem to solve or an idea to develop, they would say “Let’s start an A3!”
See a doctor in 60 minutes or less
Another project involved reviewing patients’ waiting times at NHCS’s Specialist Outpatient Clinic (SOC). To ensure that 95% of patients would be seen by doctors within 60 minutes, the project team focused on observing the flow of patients using Lean principles.
Three solutions were subsequently put forth by the team. One was the introduction of a Flow Manager, who would visit waiting areas every hour to see if there are any patients waiting beyond 60 minutes, as well as to foresee any problems or long waits. Through daily flow management, staff could have a clearer overview of their tasks for the day, as well as visibility over the flow of patients. This enables staff to take immediate corrective action if any areas were experiencing problems.
With daily flow management in place, the percentage of patients who waited for more than 60 minutes was reduced significantly from 15% to 8%.
The second solution was to review the length of patient consultations as some doctors felt that the time allocated was too short. This led to the overrunning of consultations, which resulted in the snowball effect of long waiting times for patients.
Together with doctors, nurses and operational staff, the team figured out a more realistic schedule. Since a one-size-fits-all solution would not work, they designed a customisable template, taking into account each doctor’s mean consultation time. Doctors who tended to spend more time with their patients were also given buffer slots to prevent the culmination of patients at the waiting area.
The third solution was to open the first few consultation time slots to walk-in patients. This enabled doctors to start their clinic on time instead of waiting for patients who were late for their appointments, or did not show up.
Though some doctors had initial concerns over the design approach, the team made efforts to listen and address them, and managed to drive the project on. In fact, doctors who were not involved in this particular project also came to know about the solutions and expressed an interest in replacing their appointment templates.
Lessons and takeaways
Ms Lay Sock Yee, Senior Manager, Quality Management at the NHCS, shared that the teamwork, collaboration, and the involvement of all staff in the respective areas made it possible for the teams to achieve such positive results.
“The projects had changed our perspectives and way of doing things. Before this, we did not usually come together as a diverse group of professionals to discuss common problems. Typically, we would see several uncoordinated groups spring up. Now that we’ve adopted Lean Thinking and practices, we have all come together with a common goal in mind,” she reflects.
“It is gratifying to see a growing number of people were showing curiosity about the projects when the results appeared. The project teams and line managers were able to demonstrate how this transformational approach has successfully made work easier while greatly benefitting the patients. This, in turn, will encourage more staff participation in Lean improvement work and more positive outcomes to materialise.”
Ms Junaitha Gaffoor, Senior Lecturer, SIT who interacted with the project teams through the LSDP, shares her observations, “It was very common that in the early part of the lean journey, everyone was focusing on identifying solutions. However, it is important to always understand the current state first. The key success factor for these initiatives was the commitment from the top management, hence engagement with the leaders was crucial.”
Recognising that the success of Lean transformation hinges on continuous staff engagement and a positive mindset, Ms Lay affirms, “We will continue to instil Lean Thinking into all our staff; to inculcate this as part of our culture and our management system, and embed this into the capabilities development for our staff.”
Case study adapted from 'The Learning Enterprise: Innovative Practices for Organisational Transformation', a book by NACE@SIT that documents the learning journey of four local companies to pioneer workplace learning and Lean transformation with SIT.
Header image credit: Wallpaper Flare