SIT student Dino Tan proves that embracing change will open new doors of learning opportunities.
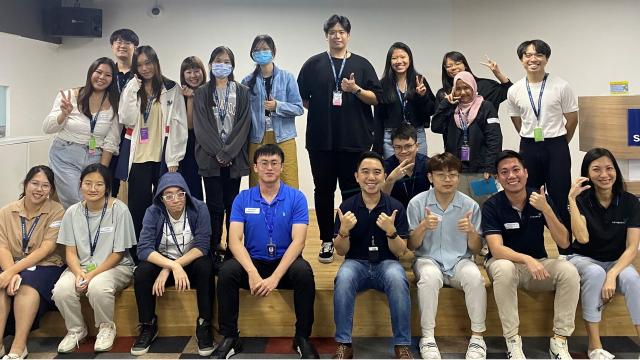
Dino Tan (second row, fifth from right) with other interns at the internship orientation at Skyworks office. (Photo: Dino Tan)
Endless lines of symbols – semicolons, parentheses and curly braces – covered the entire computer screen. Together, these lines form written code – the foundation of programming language.
This sight, which might be foreign to most, is comforting to Dino Tan. But it was not always the case. Just six months ago, he only knew the basics of written code and computer programming.
“I came from a pure mechanical engineering background and had very little programming skills,” said the final-year Mechanical Design and Manufacturing Engineering undergraduate at the Singapore Institute of Technology (SIT).
The change came during an unlikely move out of his comfort zone. Instead of sticking to his tried and tested sphere of mechanical engineering, the 26-year-old chose an internship which forced him to learn coding.
“I was keen to pursue an internship that involves technology and programming, as I would like to broaden my skill sets and deepen my understanding of contemporary engineering solutions. Recognising the growing importance of software integration within mechanical systems and disciplines in today's industry, I see it as an essential step towards becoming a more versatile engineer,” Dino shared.
As part of his Integrated Work Study Programme (IWSP), he spent six months as a visual inspection intern in the Dicing, Packing, and Shipping (DPS) department at high-performance analogue and mixed-signal semiconductor manufacturer Skyworks Solutions, Inc.
“I wanted to see how far I could go in terms of my programming skills,” he said. He went quite some way, thanks to SIT’s flagship work attachment programme, picking up not only fresh ideas but also new industry skills.
Every week at Skyworks begins with a department huddle, also known as the Toolbox Meeting. This 30-minute meeting covers key updates and activities that have been completed and upcoming tasks and projects, providing Dino an insight into daily operations and manufacturing processes.
“These meetings serve as a launchpad for me to learn and assist my teammates, as I’ll be assigned tasks during this session,” he said.
One challenge stood out for him. His mentor, Mr Chew Meng Hwee, senior process engineer at Skyworks, raised a recurring issue where data files in the visual inspection machine, which detects defects, functional flaws and irregularities in the manufacturing process of radio frequency (RF) filters, were corrupted or missing.
This severely disrupted workflow along the manufacturing line, and Dino was tasked with creating a solution. It took him months and a lot of research to develop ideas. By the end of his work attachment, he had programmed an automated system to back up important data files on a cloud server. This would prevent any data files from going missing or getting corrupted. “In the event that there are missing or corrupted fields, the engineers can easily go through the cloud server and retrieve them,” added Dino.
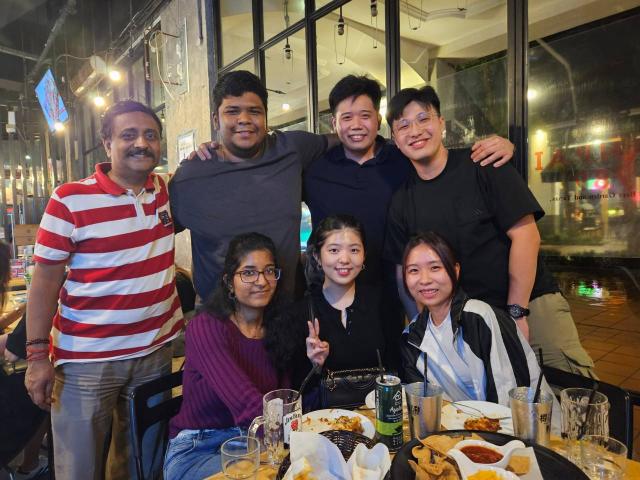
Farewell and welcome gathering for exiting Skyworks interns and new interns. Dino Tan is in the second row, second from right. (Photo: Dino Tan)
For the visual inspection machines to be able to detect flaws, their sensors need to be well-protected and in top-notch condition. This means that the microcontroller, a mini-computer that handles all the sensor data, has to be well-encased within the machine.
Dino was tasked with designing the sensor casing, a job which allowed him to step back into his comfort zone, drawing on an existing skill set – mechanical design. However, he soon realised it would not be an easy task.
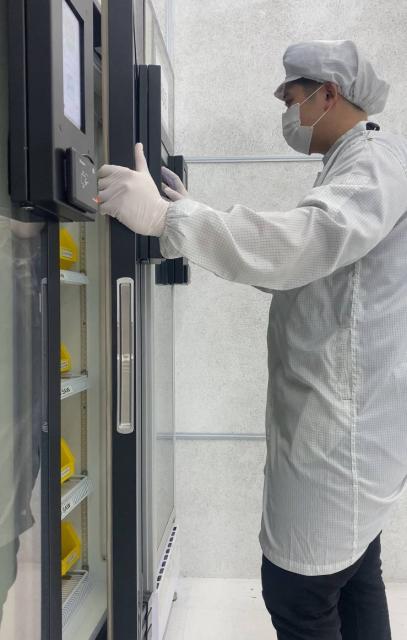
Dino Tan restocking the RFID (Radio Frequency Identification) cabinet at Skyworks. (Photo: Dino Tan)
“If I designed a simple top and bottom casing, a lot of bolts and screws would be required to hold it together. This would make it hard for engineers to disassemble the case for troubleshooting purposes,” he explained.
The breakthrough came with some help from his mentor. Mr Chew showed him a recent product he had created with Print-In-Place, a 3D printing method that can print hinges, linkage, and joints without requiring manual assembly. Dino then used the same method to design hinges for the casing.
“Mr Chew gave me the opportunity and guidance to explore new ideas,” said Dino.
Graduating in October this year, Dino will embark on the next phase of life with one invaluable takeaway from Skyworks: Don’t be afraid to try new things.
While his interests still lie in mechanical engineering within the automotive and aerospace sectors, he is open to working in the technology industry. More importantly, he relishes picking up new skills that will help him solve more complex issues to make a meaningful contribution to society.
“Before my IWSP, I thought work attachments consisted of long, mundane hours with few growth opportunities. But my IWSP at Skyworks was not the case. Every day was different, as new problems and issues arose in this dynamic industry. Aside from new programming skills, I also attained other soft skills such as adaptability and a proactive approach to problem-solving from my IWSP stint. These will serve me well for the rest of my academic term at SIT,” he said.